ANALISI METALLURGICHE
Prove di corrosione
La corrosione può essere definita come il processo che determina il degrado di un materiale metallico a seguito dell’attacco da parte dell’ambiente in cui si trova, passando dallo stato elementare allo stato ossidato. La possibilità che un processo di corrosione abbia luogo e la velocità con cui esso avviene dipendono dal tipo di metallo, dalle concentrazioni dei reagenti e dei prodotti di reazione, dalla temperatura e da altri fattori quali le sollecitazioni meccaniche e dai fenomeni di erosione.
Per una corretta progettazione delle apparecchiature e degli impianti occorre valutare la capacità di un prodotto di resistere alla corrosione. Nel settore automotive la verifica della capacità di un componente di resistere alla corrosione ha assunto negli ultimi anni una notevole importanza sia nella fase di ricerca e sviluppo che fase di qualifica e collaudo dei materiali.
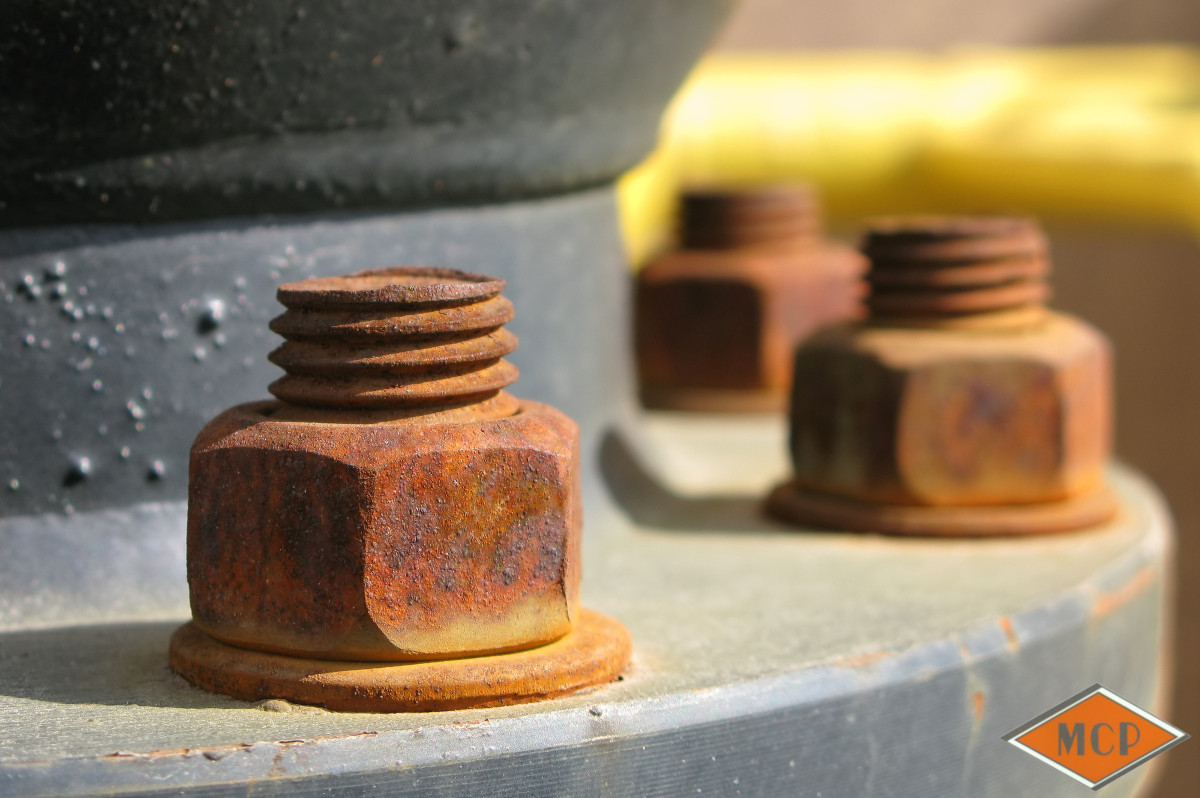
Prove di corrosione eseguite dal nostro laboratorio
Il laboratorio metallurgico ed il reparto Automotive di Modena Centro Prove dispongono di una vasta gamma di tecnologie che permettono l’esecuzione dei seguenti test:
- Nebbia salina neutra NSS
- Nebbia salino acetica ASS
- Nebbia cupro salino acetica CASS
- Camera umidostatica
- Corrosione ciclica
Le prove di corrosione in nebbia salina, gli invecchiamenti accelerati in camera umidostatica e i cicli di corrosione ciclica sono eseguiti in accordo alle principali norme internazionali.
Test di Corrosione | Normativa di riferimento |
---|---|
Nebbia salina neutra (NSS) Nebbia salino acetica (ASS) Nebbia cupro salino acetica (CASS) | UNI EN ISO 9227: Prove di corrosione in atmosfere artificiali - Prove in nebbia salina |
ASTM B117: Standard Practice for Operating Salt Spray (Fog) Apparatus | |
ASTM B368: Standard Test Method for Copper-Accelerated Acetic Acid-Salt Spray (Fog) Testing (CASS Test) | |
FIAT 50180: Prove di corrosione | |
Camera umidostatica | UNI EN ISO 6270-2: Pitture e vernici - Determinazione della resistenza all'umidità - Parte 2: Procedura per l'esposizione di provini ad atmosfere di acqua di condensa |
ASTM D1735: Standard Practice for Testing Water Resistance of Coatings Using Water Fog Apparatus | |
DIN 50017: Condensation Water Test Atmospheres | |
Corrosione ciclica | SAE J2334: Laboratory Cyclic Corrosion Test |
PV 1210: Body and Add-On Parts/Hang-On Parts - Corrosion Test | |
CNH MTM0106: Cyclic Corrosion Test |
I risultati delle prove di corrosione eseguite sui rivestimenti organici (vernici) possono essere valutati secondo le seguenti norme internazionali:
- UNI EN ISO 4628-2: Valutazione del grado di blistering
- UNI EN ISO 4628-3: Valutazione del grado di arrugginimento
- UNI EN ISO 4628-4: Valutazione del grado di screpolatura
- UNI EN ISO 4628-5: Valutazione del gradodi sfogliamento
- UNI EN ISO 4628-6: Valutazione del grado di sfarinamento con il metodo del nastro adesivo
- UNI EN ISO 4628-8: Valutazione del grado di propagazione della corrosione attorno a un’incisione
- UNI EN ISO 4628-10: Valutazione del grado di corrosione filiforme
- ASTM D1654-08: Standard Test Method for Evaluation of Painted or Coated Specimens Subjected to Corrosive Environments
- ASTM D714-02: Standard Test Method for Evaluating Degree of Blistering of Paints.
La corrosione
La corrosione dei metalli può essere considerata come il processo opposto alla metallurgia estrattiva. Le leghe e i metalli raramente si trovano in equilibrio in condizioni ambientali standard. La maggior parte dei metalli sono presenti in natura sotto forma di ossidi, solfati, carbonati o silicati. I metalli combinati in questi composti sono più stabili rispetto ai metalli puri e quindi vi è una tendenza spontanea dei metalli a reagire chimicamente per ritornare nello stato di ossido o sale. La corrosione è, pertanto, un processo spontaneo, irreversibile e naturale che genera la degradazione delle caratteristiche e proprietà fisiche del materiale.
Il prodotto che viene generato dalla corrosione del ferro è l’ossido di ferro, comunemente chiamato ruggine. La maggior parte dei fenomeni corrosivi dei metalli è conseguenza di attacco di tipo elettrochimico che avviene in ambiente umido (soluzioni acquose o ambiente atmosferico). I metalli possono anche corrodersi a seguito di fenomeni di ossidazione ad alta temperatura (corrosione a secco).
Per un progettista, la corrosione è un processo distruttivo che rappresenta un enorme perdita economica; pertanto risulta fondamentale essere a conoscenza delle tecniche di controllo e prevenzione della corrosione, anche attraverso prove e simulazioni in laboratorio. Un’errata valutazione del materiale da impiegare e dell’ambiente di utilizzo, porterebbe a:
- DANNI MECCANICI: la corrosione può provocare il deterioramento irreversibile delle caratteristiche meccaniche di tutti i componenti che sono sottoposti a fatica come braccetti, staffe e alberi di trasmissione.
- DANNI ESTETICI: la corrosione induce un forte degrado a livello estetico, requisito fondamentale nel settore dell’auto.
- DANNI STRUTTURALI: la corrosione può essere la causa principale di malfunzionamenti elettrici e meccanici per quanto riguarda civile e architettonico
- DANNI AMBIENTALI: la corrosione può rilasciare sostanze tossiche e inquinanti nell’ambiente che ci circonda.
Nebbia Salina
La prova in nebbia salina (Salt Spray Test) è un metodo di prova standardizzato, utilizzato per verificare la resistenza alla corrosione dei materiali e dei rivestimenti. Solitamente, i materiali da testare sono campioni metallici e rifiniti con un rivestimento superficiale, che ha la funzione di fornire al metallo sottostante una protezione dalla corrosione e di rendere esteticamente gradevole il campione.
La prova di nebbia salina è un test che produce un’aggressione superficiale accelerando la comparsa di corrosione sui campioni analizzati. La comparsa della corrosione, comunemente chiamata “ruggine”, viene valutata dopo un periodo di tempo scelto sulla base delle normative o concordato col cliente in base al rivestimento sottoposto a test.
Spesso il rivestimento viene inciso localmente al fine di provocare una debolezza artificiale nel rivestimento, per verificare il comportamento dello stesso in prossimità del graffio. Più il rivestimento è resistente, più lungo sarà il periodo di prova in nebbia salina prima della comparsa di corrosione. Questi test permettono di conoscere il livello di resistenza alla corrosione dei materiali o dei rivestimenti consentendo di verificare se occorre apportare modifiche al progetto, al fine di garantire standard più elevati di resistenza all’invecchiamento accelerato.
Le condizioni corrosive all’interno della camera prevedono temperatura e umidità costanti per tutta la prova, in un ambiente saturo di umidità. In questo modo si forma un velo di umidità costituito da acqua e sale che, depositandosi sul campione in esame, funge da elettrolita e permette le reazioni di dissoluzione del ferro e la conseguente formazione dell’ossido di ferro (ruggine). I risultati della prova di nebbia salina, solitamente valutati in modo visivo, sono:
- il tempo di comparsa dei fenomeni corrosivi (siano essi ruggine rossa, ossido bianco o punti neri in base alla natura del materiale),
- la tipologia della corrosione (puntiforme, generalizzata, cricche, bolle…)
- la quantità dei prodotti di corrosione.
- Propagazione dei fenomeni ossidativi nell’intorno dell’intaglio provocato sul rivestimento
La prova di resistenza in nebbia salina non serve per dare un’indicazione di durata nell’ambiente reale ma per avere un parametro ripetibile: per giudicare la resistenza di un rivestimento o di un materiale in ambiente corrosivo o per effettuare un confronto tra materiali differenti e determinare la conformità rispetto a uno standard definito.
Una tipologia di nebbia salina considerata ancora più aggressiva è la cupro-salino-acetica. In questo tipo di test si sostituisce la soluzione salina con una soluzione anch’essa a base di cloruro di sodio ma arricchita con acido acetico e un sale rameico. La presenza di queste ulteriori componenti, che peraltro abbassano il pH, rende estremamente più aggressivo l’ambiente di reazione così da simulare situazioni estreme di corrosione sui particolari testati.
Camera Umidostatica
L’umidità è in grado di innescare fenomeni di corrosione del materiale o di degrado del rivestimento (blistering, cracking, flaking, etc.).
Il test in camera umidostatica è molto richiesto per la valutazione della qualità delle verniciature secondo ISO 6270-2: “Pitture e vernici. Determinazione della resistenza all’umidità. Procedura per l’esposizione di campioni di prova in atmosfere a condensazione d’acqua –Paint and varnishes. Determination of resistance to humidity. Procedure for exposing test specimens in condensation-water atmospheres” e normative equivalenti.
La camera è a tenuta stagna per impedire la fuoriuscita dei vapori e fabbricata con materiali resistenti alla corrosione per non influire sui materiali da analizzare. Il posizionamento dei campioni deve seguire le indicazioni specificate nella normativa per garantire che la condensa scivoli correttamente dalle pareti o dal soffitto della camera e non da un campione all’altro:
- i campioni devono essere sufficientemente distanziati
- l’angolo di inclinazione deve essere maggiore o uguale a 60°, in modo da permettere alla condensa depositata di scivolare via
- temperatura e umidità omogenee in tutta la camera.
La prova termina al raggiungimento di una durata stabilita o nel caso in cui si verifichi un degrado nel materiale tale da comprometterne la conformità.
Corrosione ciclica
Per simulare meglio le reali condizioni di utilizzo di un componente, o nel caso la normativa lo richieda, si può optare per effettuare un test di corrosione ciclica. In questo test si verifica la resistenza a corrosione di un materiale, sottoponendolo, anziché ad un unico tipo di corrosione uniforme, a diverse fasi di esposizione, che prevedono l’alternarsi di cicli di normale nebbia salina, a cicli di sola esposizione all’umidità (senza la componente salina) a cicli di asciugatura e riposo.
Saranno le normative (come ad esempio le SAE J2334, PV 1210, CNH MTM0106) di volta in volta a descriverci quanti cicli sottoporre i campioni e per quanto tempo le varie fasi andranno protratte. I criteri di valutazione al termine dei cicli di corrosione sono comparabili con quelli adottati per la nebbia salina e valutano rapidità di formazione, quantità e tipologia dei fenomeni corrosivi. Anche in questo caso, se la normativa lo richiede, il rivestimento viene manualmente inciso al fine di verificare il comportamento del particolare nel suo intorno.